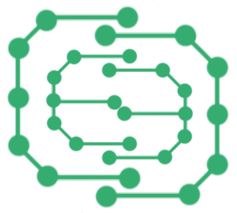
29 maggio 2024 – Tra giugno e settembre 2024, gli altiforni dell’acciaieria Tata Steel di Port Talbot, in Galles, verranno spenti per sempre. La Tata Steel, multinazionale indiana del siderurgico, ha annunciato che saranno sostituiti con dei forni elettrici, meno impattanti sull’ambiente. La trasformazione porterà, secondo le stime dei sindacati riportate dal Guardian, la perdita di 2.800 posti di lavoro. Quelli, al contrario degli altiforni, non saranno sostituiti.
Come mostra il caso di Port Talbot, la transizione ecologica dell’industria siderurgica è un percorso tortuoso. Parte dall’abbandono del carbone, finisce con l’idrogeno verde e, nel mezzo, richiede un aumento dell’uso del gas e un calo degli occupati, perché per i forni elettrici serve meno manodopera.
Oggi, la produzione di acciaio in Ue vale il 5 per cento delle emissioni (7 per cento a livello globale) e 2.5 milioni di posti di lavoro tra diretti, indiretti e indotto. Come il trasporto aereo, è uno dei settori definiti hard to abate, cioè le attività con le emissioni di CO₂ più difficili da ridurre. L’arrivo a una produzione di solo acciaio “verde” è una sfida complessa che tocca aspetti tecnologici, economici e sociali. Proviamo a capire se e come l’Europa li sta affrontando.
Nel 2024 l’acciaio si produce in due modi. C’è la siderurgia primaria, o ciclo integrale, che utilizza gli altiforni: questi enormi impianti sempre accesi combinano il minerale di ferro con il coke, cioè carbone cotto, per produrre ghisa liquida, che poi viene convertita in acciaio primario da un forno a ossigeno di base. È il metodo tradizionale, quello che la Tata Steel abbandonerà a Port Talbot.
Poi c’è la siderurgia secondaria: dei forni elettrici ad arco fondono il rottame, cioè dei rifiuti ferrosi, per produrre acciaio. L’acciaio è infatti un materiale completamente riciclabile.
La produzione con altiforni offre un acciaio più puro ma ha un enorme impatto ambientale. Secondo uno studio sulla decarbonizzazione dell’industria siderurgica della Fondazione Di Vittorio, un ente di ricerca della CGIL, la produzione di una tonnellata di acciaio genera con il ciclo integrale oltre 2 tonnellate di CO₂, a fronte di 0.135 tonnellate con i forni elettrici. Il ciclo integrale comporta anche maggiori consumi di acqua e suolo, mentre i forni elettrici hanno, ovviamente, consumi di energia più alti.
Questo grafico mostra il confronto dell’impatto su emissioni e consumi dei due modelli di produzione.
Il ciclo integrale è il modello più diffuso nella siderurgia mondiale, dominata dalla Cina. Mentre l’Italia, il secondo produttore di acciaio in Europa, si trova in una situazione inversa: Taranto è l’unica città dove si fa ancora acciaio primario con altiforni, con circa il 16,5 per cento della produzione nazionale. Il resto dell’acciaio viene fatto nei forni elettrici, soprattutto da PMI lombarde.
Ma come si rende l’acciaio verde? Il problema è complesso. Per raggiungere l’obiettivo europeo di taglio dell’80-95 per cento delle emissioni del siderurgico nel 2050, non c’è una soluzione unica e pronta su larga scala, ma serve l’adozione contemporanea di più strategie.
Una è favorire il riciclo dell’acciaio, aumentando sempre di più la siderurgia secondaria che, come visto, inquina meno. Un’altra è la creazione di sistemi di cattura e stoccaggio dell’anidride carbonica, cioè quelle tecnologie, ancora in fase sperimentale, con cui si spera di poter compensare tutte le emissioni non rimovibili.
Altra strada importante è l’aumento dell’uso del preridotto o DRI (Direct Reduced Iron): si tratta di un materiale ferroso che subisce una riduzione diretta con gas naturale, carbone o idrogeno, senza dover passare attraverso la fusione. Può essere impiegato sia negli altiforni sia nei forni elettrici al posto del rottame, in entrambi i casi con minori emissioni climalteranti.
Se poi la riduzione del DRI avviene con idrogeno verde, prodotto da fonti rinnovabili, le emissioni sono nulle: il minerale ferroso (ossido di ferro) non cede più l’ossigeno al carbonio producendo CO₂, ma all’idrogeno, producendo acqua. In questo caso, è quindi corretto parlare di “acciaio verde”, realizzato con zero emissioni di anidride carbonica.
L’acciaio prodotto da DRI e idrogeno verde nei forni elettrici è l’obiettivo finale della strategia Ue per la decarbonizzazione del settore siderurgico, ma la strada è ancora lunghissima: oggi, l’acciaio verde viene fatto soltanto da progetti pilota con produzioni limitate, in particolare nel Nord della Svezia, dove c’è alta disponibilità di rinnovabili. Al 2030, il piano REPowerEU punta a rendere “verde” circa il 30 per cento dell’acciaio primario.
Tutto questo va poi fatto mantenendo la competitività della siderurgia europea, già in crisi per il caro energia causato dalla guerra in Ucraina. È possibile? I problemi sono tanti e di varia natura, come emerso durante il convegno di Legambiente “L’acciaio oltre il carbone” a Taranto.
C’è intanto un tema di materie prime. Abbandonare gli altiforni per i forni elettrici richiede una crescita della domanda del materiale ferroso per gli impianti DRI e di rottame di acciaio, entrambi poco disponibili sul mercato. Vuol anche dire aumentare i consumi di gas, prima, e di energia rinnovabile, poi, con tutte le relative incognite legate ai costi. La filiera dell’idrogeno verde, su cui l’Europa sta comunque investendo molte risorse, è di fatto un mercato ancora da costruire.
La stessa Ue riconosce che i costi di produzione dell’acciaio da DRI e idrogeno verde potrebbero diventare competitivi soltanto intorno al 2050, quando, si presume, i costi delle rinnovabili saranno minori e produrre con fonti fossili non converrà più. A livello normativo, due misure dovrebbero aiutare il siderurgico in questo senso.
Fonte: substack.com